江淮追梦人| 弯道跑出“加速度”
【汽车焦点 快讯】
没有行业标准,就拿废旧集装箱当做临时试验室;爆破试验5000次,只为电池包拿到100%通关卡……从入职之时即加入新能源汽车产品研发工作,江淮汽车新能源乘用车公司新能源汽车研究院院长助理赵久志,见证了第一代电动车iEV1以来的江淮新能源乘用车快速成长之路。他透露,目前江淮汽车已经实现500公里续航技术,到2025年,电动车有望和传统燃油车达到成本持平,更多走入百姓家。
一个电池包开发投入两年半时间
在汽车行业,江淮汽车涉足新能源汽车最早,也是最富成效、产业化推进速度最快的整车企业。
2006年7月,赵久志进入江淮汽车技术中心,从事纯电动车产品研发工作。2010年,第一代电动车iEV1投入市场示范运行,首批591辆上路,开启了国内推广新能源电动车产业化的先河。
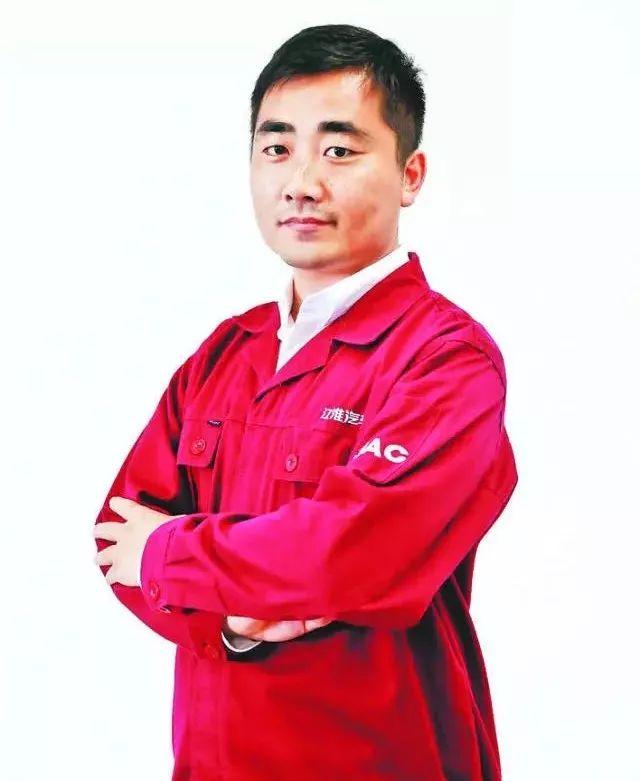
*江淮汽车新能源乘用车公司新能源汽车研究院院长助理赵久志
“在新能源汽车研发上,江汽是国内起步比较早的企业。当时公司经过反复的研究,明确了纯电驱动的技术路线。”赵久志说。作为一个新兴事物,电动车的发展需要在各个领域的不断创新来支撑。其中,电池是阻碍其发展的巨大瓶颈。“为了追求长续里程,我们要不断地追求电池的能量密度。然而,能量越高一旦发生安全事故,安全性的危害就会越大。所以,安全性的开发是一个前提,不解决安全问题的能量密度不是真正的创新,不是真正的技术进步。所以我们在电池的开发过程中始终将安全作为研发的主线。”
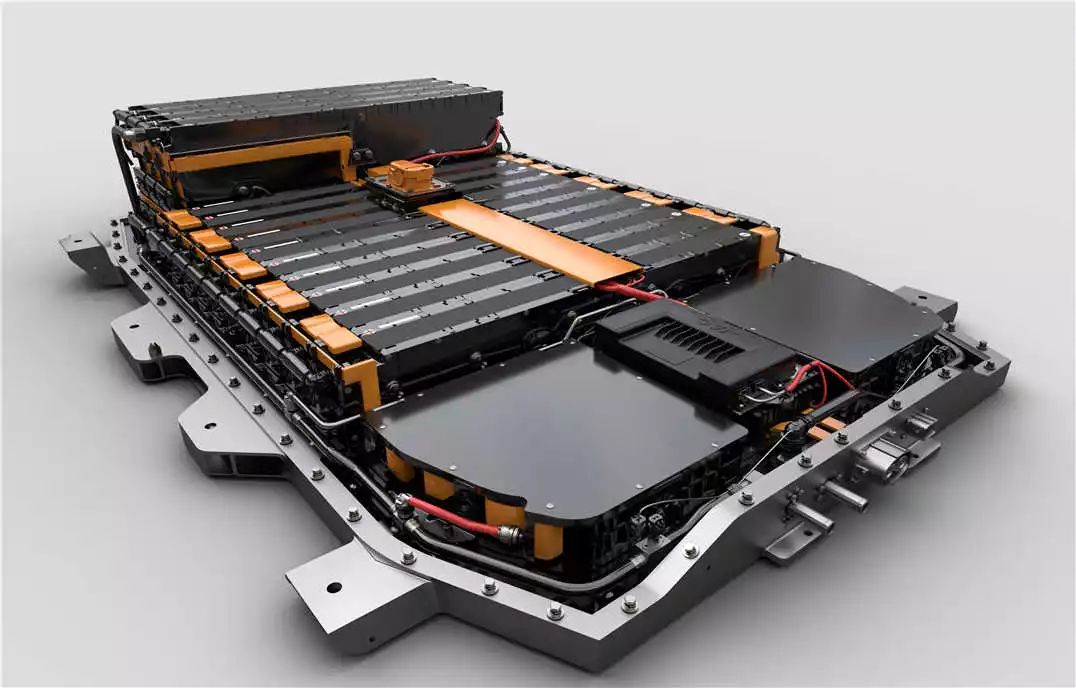
*动力电池包
赵久志说,在电池领域研发上,江汽投入很大。一款车一个电池包的开发大概需要两年半的时间,累计研制电池包近百套,研发投入从成组的数据开发、试制到试验,需要上千万元。“只有这种投入,大量的试验验证才能保证产品是安全的,是可靠的。”
废弃集装箱变身临时爆破试验室
第一代电动车iEV1使用的是磷酸铁锂电池,安全性好、寿命长,但缺点在于能量密度低,整车只能跑100公里。“2014年前后,很多企业开始尝试使用能量密度更高的三元电池,但它的安全性不够好,必须要先攻关热失控安全问题。”赵久志告诉记者,在电池研发上,从单体到模组到电池包,都是按照江淮技术攻关V字型流程和整车到产品开发NAM流程,严格分阶段、按节点开展相关的样品测试工作。
“我们把电池包中的一个单体引爆,看看整个电池包会不会起火爆炸。在第一声爆破后,如果紧接着再有‘嘭’的一声,心情就立刻沉下去,因为试验失败了。”赵久志告诉记者,由于行业暂无标准,没有试验室可以承担爆破测试,因此这个试验是在野外的废旧集装箱中完成的,条件艰苦。“因为这个‘临时试验室’唯一的电器就是一个电灯,大家就只能在集装箱的附近等待,尤其寒冬酷暑,滋味并不好受。”
*液冷恒温技术
从集装箱拿到失败样品,团队就立刻在附近开展检查测试。“我们给自己定了一个标准,每一个量产的产品,要连续通过100次、100%通过的试验后才能批量生产。”就这样,赵久志和他所在的团队,反复做了5000次试验,终于找到了规律。
坚持以安全作为电池研发前提
通过近十年不断攻关,江汽在国内率先取得热失控防护技术突破,基本上实现了热失控的本质安全,在国内率先取得突破,实现了电池包电芯爆炸后不起火,结合世界领先的热管理液冷技术,杜绝了电池安全风险。
*江淮新能源第八代技术第三代产品iEVS4
“现在,第八代技术第三代产品iEVS4的续航里程已经达到了400公里以上,而在试验室中,我们已经掌握了500公里的续航里程技术,这在行业中是领先水平。”赵久志告诉记者,目前城市出行的日里程需求,绝大多数在50公里左右,目前新能源汽车的续航里程已经可以满足“一周充一次电”的需求,在确保安全的情况下,技术团队也在不断尝试提升电池和整车性能。“在此过程中,循环寿命、安全性、成本、快充性能,是我们一直在攻克的难点。”赵久志透露,在不考虑新能源汽车补贴的情况下,电动车和燃油车的综合使用成本将在2025年前后持平,届时,将迎来新能源汽车市场大规模批量产业化的春天。