【汽车焦点 快讯】
工业4.0是近几年非常耳熟能详的概念,这个名词也意味着工业上出现的新要求、新变革,其核心特征是互联,它颠覆了人们的传统思维,开辟了汽车行业全流程智能化的先河。
前不久,江铃集团新能源耗时3年在江西南昌打造的能量工厂开始启用。正是工业4.0时代下的产物,工厂中现代化的智能数字,充满温度的同时让人惊叹。政府、行业专家到这个工厂参观,纷纷竖起了大拇指。
在人们的印象里,汽车工厂是一个既热又脏又乱的地方。而在这个工厂里,工作人员几乎看不到,地面干净整洁,几乎看不到一处脏乱的地方。整个厂区像一座花园,如果不走进车间,很难看出这是一家造车工厂。

走进江铃集团新能源能量工厂,犹如走进了科幻现场。
工厂分冲压、焊装、涂装、总装四大生产工艺以及动力电池生产线五个环节,每个车间布局均呈U字形,布局合理,工艺链顺畅完整。
我们就拿焊装来说,其采用了8种连接工艺,包括国际领先的FDS摩擦驱动、SPR自冲铆接技术、CMT冷金属过度保护焊等新型连接工艺,可以说是国内第一家大规模实现钢铝及复合材料异种材料连接的工厂。
更让人惊奇的是,焊接线191台工业机器人可在专业工程师的监控下,有条不紊的运作,焊接自动化率可达90%以上。工艺采用柔性GATE库总拼夹具,车型自动切换且切换快速,实现四车型共线生产。涂胶工艺采用在线视觉监测系统,且具备大数据分析功能,可实时监控产品质量。
车间还采用自适应焊接系统(焊枪自动夹紧)、智能辅助装置(物件助力臂)等节能设备,降低工厂能耗,打造绿色节能工厂。
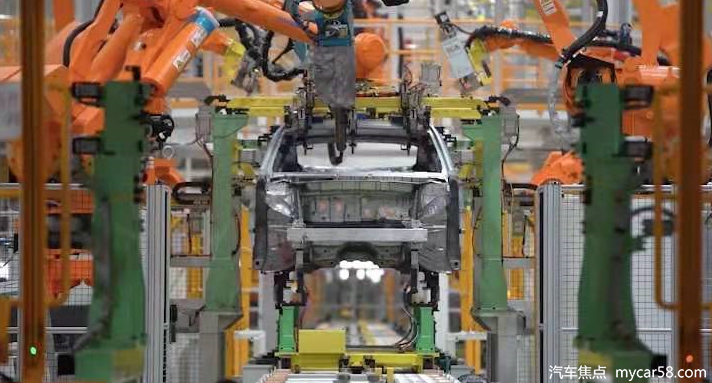
江铃集团新能源焊装厂设计以智能、高效、节能、环保为理念,实现生产数字化、柔性化。工厂焊装车间的自动化率达到了85%,主焊部分的自动化率高达90%,涂胶部分自动化率高达100%。
涂装车间喷涂工艺自动化率100%,堪称国内一流水平。
而总装车间智能物流配送系统,是国内首个实现全无人配送的纯电动汽车总装车间,并应用LES系统智能调度50台物料配送AGV,完成物料自动配送。
工厂整体采用了人、车、物分流的设计,极大降低了意外、事故的发生概率。其次设计有专门的运输通道,使得生产、物流运输的效率得到了很大的提升,同时也是优化了各专项路线,使得运输的损耗、时间成本得到降低。工厂采用信息化监控,实现设备状态、产品质量、能耗数据实时监控和分析,可自动调整生产顺序,做到柔性生产,量化时间,快速响应市场需求。

新工厂按照工业4.0标准建设,全工厂布置光伏发电系统,在天晴的时候,通过光伏系统,可以满足生产、办公区用电,做到零消耗。厂房设计合理增大采光面积并结合光伏发电系统,使得晴天无需开灯。
雨水回收、余热利用、废气处理等多方面做到了最大程度资源利用,不但降低了能耗,还减少了排放。
江铃集团新能源这座智能化的能量工厂,据悉投产后可实现多平台、多车型的柔性化定制化生产。这座为工厂为企业打造了中国唯一覆盖A00级——A+级细分市场电动合资品牌、提供电动出行解决方案贡献了不竭动力,也恰是中国制造业正在经历生态变革机遇的一种有力写照。